A road train comes, through shimmering mirages of heat. Road temperatures well above 50 degrees centigrade. Air temperatures at 50 degrees. The blazing white of the fridge vans pass with a blast of furnace-hot air.
Outback Australia. Inside those Maxi-CUBE fridge van walls settle frozen goods, chilled vegetables, ice cream, all making life bearable in the hot months of North Queensland, the Territory, the Kimberley.
A world away in the very different climate of Victoria, Freighter Group employees work to keep those far-travelling goods cold and safe.
People like Gavin Lewis, a fibreglass expert who supervises the construction of the insulated panels that become a protective fortress against the North’s heat.
Gavin is the Production Supervisor at the Freighter Group panel manufacturing facility at Hallam in Eastern Victoria. It is here that the magic mix of foam and fibreglass are built to withstand the blistering heat encountered by Australian road conditions.
The balance is obvious, highly efficient insulation with low weight and high strength to take on the nation’s worst. Working in unison with efficient low weight diesel powered fridge units, Maxi-CUBE trailers roll over millions of trailer-kilometres every week.
“We start by making the foam, we’ve got our own foam machine. It’s formed into the required sized rigid modules for strength and used throughout the factory,” Gavin Lewis explains.
The rigid foam is bonded between two fibreglass skins, a laminated panel with low tare and high strength. They then go through a finishing process.
The completed panels, up to 14 metres in length, are assembled on an A frame for transport and delivered to Freighter Group’s trailer manufacturing facility in Ballarat.
Supervising the panel manufacture is what Gavin Lewis does. Moves around the floor, a bit of support here, a little guidance there. He back-fills any position in the factory when a team member is away.
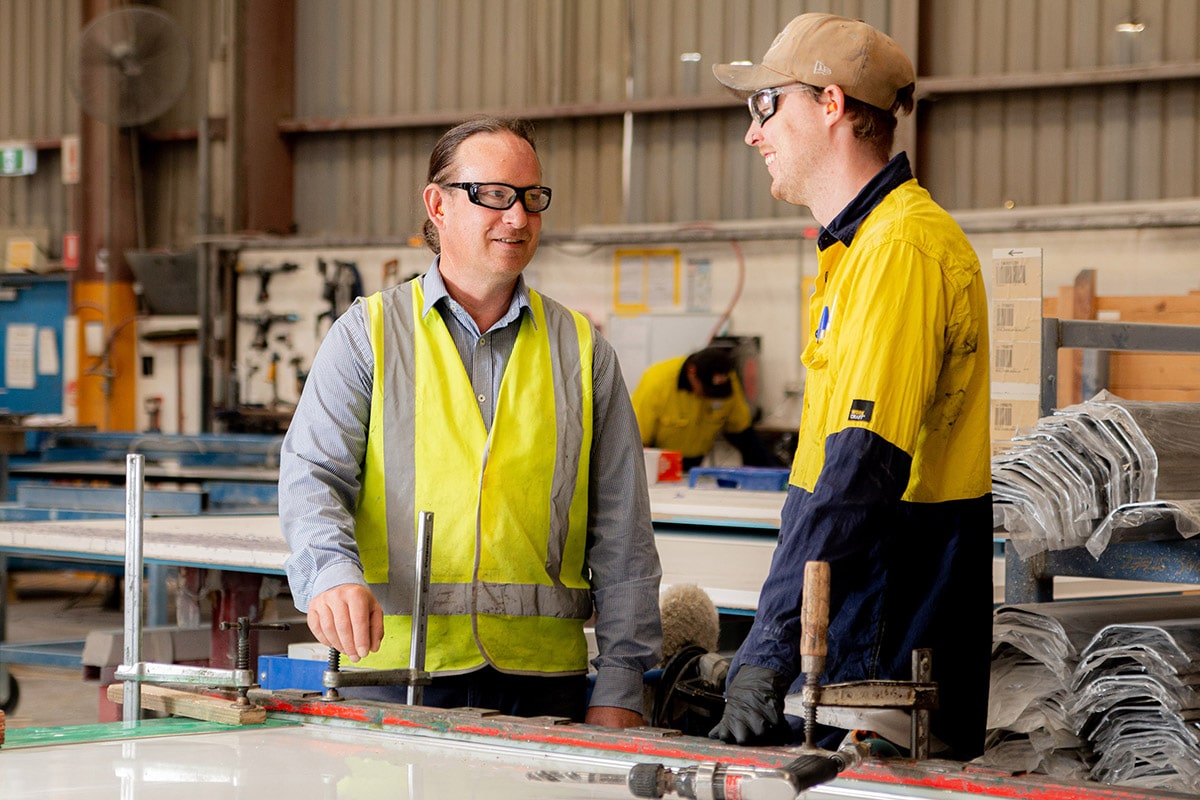
Gavin Lewis supervising staff at MaxiTRANS Hallam Panels Gavin provides support and guidance for staff at MaxiTRANS panel manufacturing facility for Maxi-CUBE trailer wall panels.
Panels aren’t a one-size fits all affair. Different build specs are made for different applications.
Wall panels on the Maxi-CUBE Classic Reefer refrigerated van have 40 mm wall thickness and 125 mm thick roof panels. While a Hi-CUBE Reefer van for fresh produce has 25 mm walls and a 100 mm roof.
Seven years ago, Gavin applied for, and got, the job at Freighter Group. He had worked in smaller outfits, making fibreglass fairings for four-wheel drives and recreational vehicles, making fibreglass aircraft components.
Hitting middle age he decided he needed experience in a large corporation so he could learn the corporate way. So he came to, and was welcomed by, Freighter Group.
Listening to Gavin, he loves being a supervisor where he can help, guide. Treat team members with sensitivity and care while at the same time being firm on production expectations.
This is what he wanted… and found with Freighter Group.
His aspiration for the future: “I just want to be the best supervisor I can possibly be.” He’s the sort of bloke who would come to work every day with a smile on his face.
While the bulk of the manufacturing at Hallam goes to in-house supply to Freighter Group’s needs, products for the PanelMASTA brand are also built in the facility.
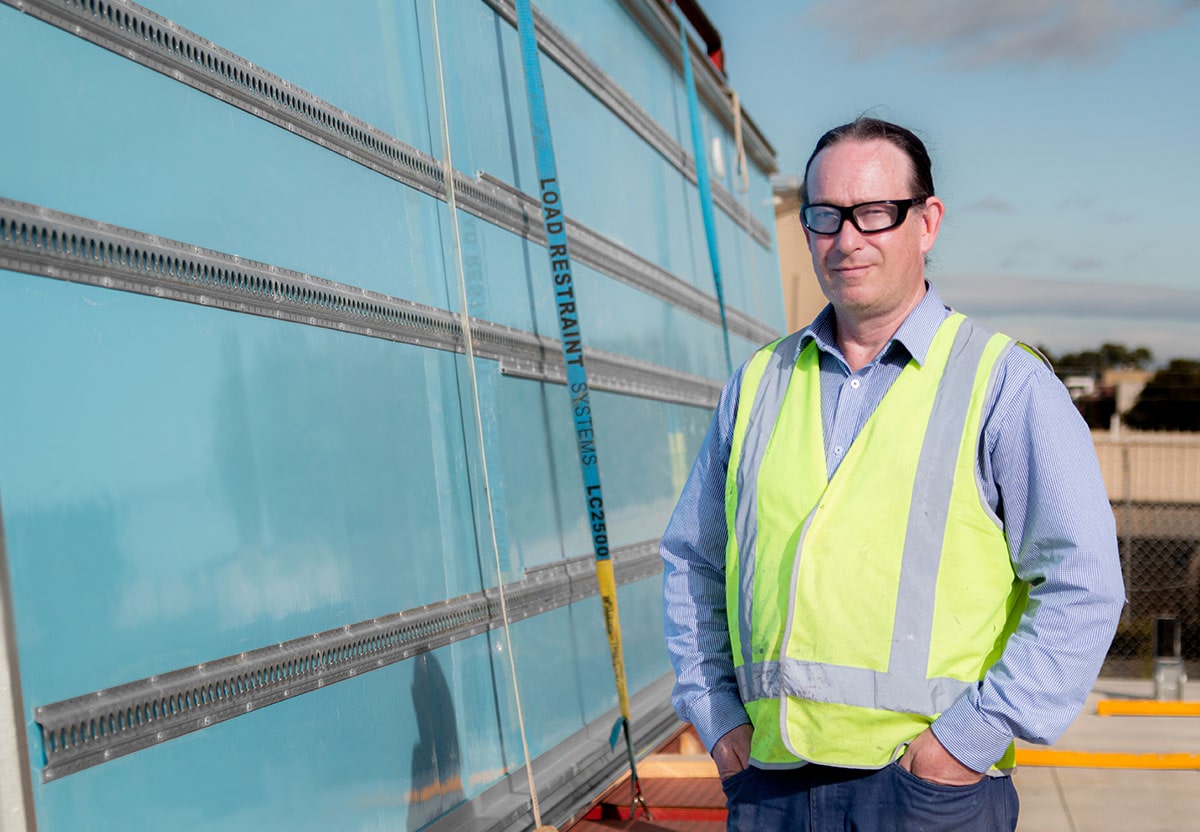
Gavin Lewis Maxi-CUBE wall panels Gavin says he wants to be the best supervisor he can be, with MaxiTRANS giving him the opportunity to continue to grow.
Gavin says these panels are mostly built to a customer’s specifications and could be for anything from repairs to a trailer rollover through to panels for body builders fitting out smaller trucks.
He says these panels are built on the same factory floor as the big Maxi-CUBE products. But there are variants.
“In some cases we use honeycomb core rather than foam depending on application. And we also build panels with high density foam. The foam core is thinner but of a higher density. We call it UltraPanel.”
Gavin Lewis says the biggest challenge working in a large facility is staffing.
“Managing the people, managing them correctly, making sure that I’m doing the right thing and learning to change with the times. Freighter Group has given me the opportunity to be a better supervisor.”
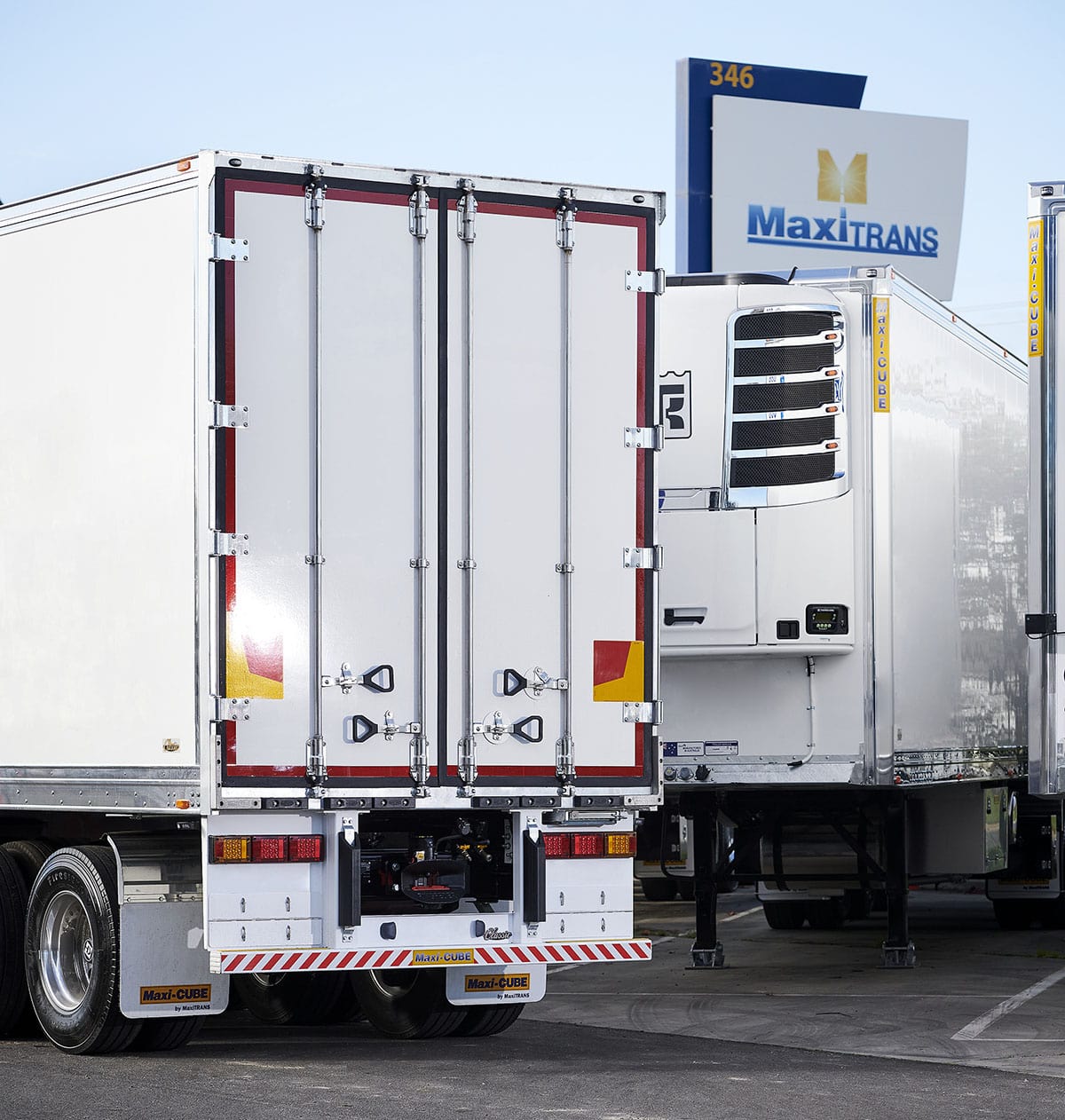
Maxi-CUBE refrigerated trailer vans MaxiTRANS Finished Maxi-CUBE trailers awaiting customer delivery after manufacturing is completed at MaxiTRANS’ manufacturing facility in Ballarat, Victoria.
Away from work Gavin has a passion for model aircraft construction.
“Nearly every night I am working on my scale models.”
He enjoys fishing and archery and with his wife they have Kandy the cat.
“Awesome,” he says of the family cat. “Kandy follows me around everywhere when I’m at home.”
With his love of aviation, he uses spare time applying his fibreglass skills to aircraft.
Gavin Lewis has come a long way from learning the fibreglass craft by making remote control boats, planes and car parts as a teenager. He has invested his life in honing and building those skills and now finds occupational fulfilment working on the big fibreglass work that is integral to a Maxi-CUBE refrigerated van, distributing the needs of life across Australia through its millions of kilometres of operation.